How does the LPG installation work?
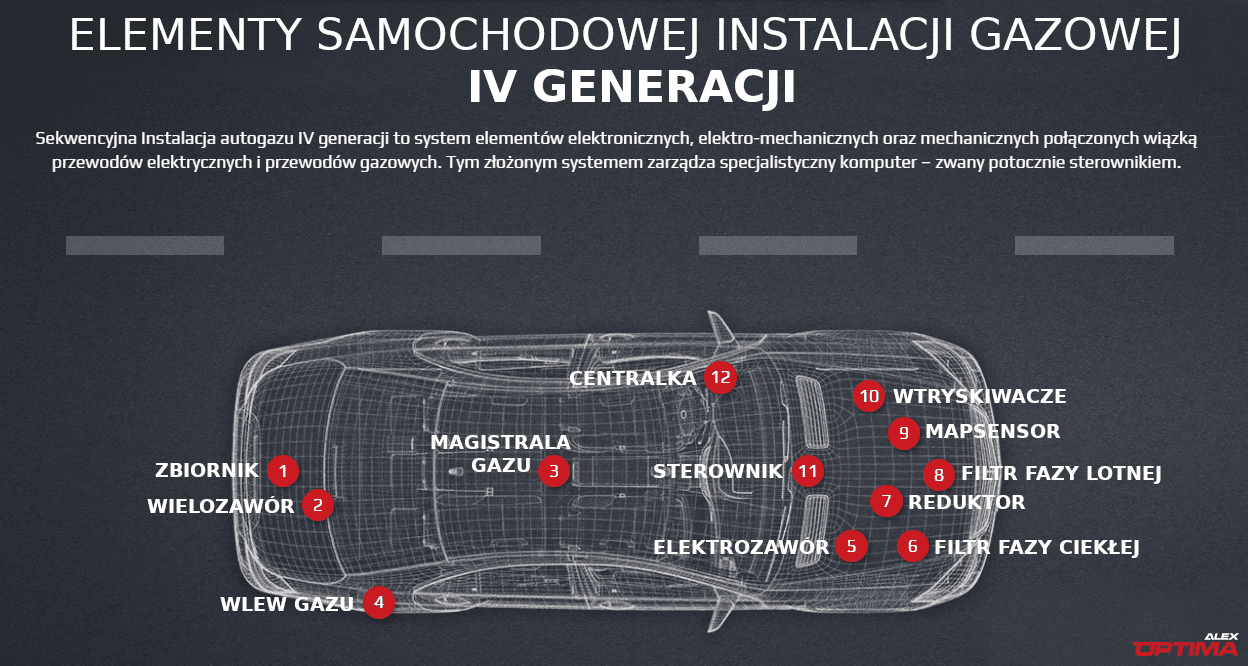
When is it recommended to install a sequential gas installation?
4th generation LPG is a vapor phase gas supply installation through electronically controlled gas injectors (operating very much like gasoline injectors). It is designed for engines with multi-point petrol injection, catalytic converter and lambda probe as well as EOBD / OBDII diagnostic systems, which require very precise fuel dosing.
This type of installation works with most engines – both with indirect injection and direct injection, turbocharged or without turbines. Prices range from PLN 2,400 to even PLN 6,000, depending on the type of engine (direct injection requires more advanced components), number of cylinders and installation class.
Sequential installation is the most common type of LPG installed today. The fact that the shortcomings of older generations were eliminated certainly contributed to this. When driving on a proven, properly installed LPG installation, you will not experience differences between the operation (power and dynamics) of a gas-powered engine and gasoline.
What distinguishes a sequential gas installation from the rest ?
The main difference between older generation gas installations and sequential installation is the use of exactly as many gas injectors as there are in the engine cylinder .
The principle of operation of the sequential gas installation
LPG filled with the filler is stored in a tank. Then the multivalve opens and releases the fuel under high pressure for a long journey. The liquid gas travels the gas line located under the car, flows into the gas solenoid valve, and after initial cleaning – into the reducer. At this point, evaporation takes place and the gas pressure is reduced to about 2 bar. The gas in the volatile phase goes to the volatile phase filter, where the second stage of cleaning from impurities takes place. Clean prepared gas goes straight to the injectors and finally enters the intake manifold (to each intake channel separately) and engine combustion chambers. The moment of feeding gas to individual channels of the intake manifold is the same as the sequence of engine operation on petrol. The brain of the whole operation is an advanced control computer – controller. As the installation director – he controls the solenoid valves, monitors gas parameters (temperature, pressure), determines the opening / closing times of the injectors (they can be different for separate cylinders) and ensures a smooth transition between fuel types (when you press the petrol / gas button). The last element is just ‘this button’ – switchboard installed in the driver’s cabin.
Elements of the 4th generation gas installation
Sequential gas injection installation (4th generation) consists of the following elements:
1.The gas tank
can be mounted inside or outside the vehicle. Typically, passenger cars are fitted with toroidal tanks – mounted in the spare wheel well and cylindrical tanks – mounted in the luggage compartment.
2. The multivalve
controls the process of refueling the gas into the tank and its flow to other parts of the system. Operation is based on simple and reliable mechanical solutions, which makes the use of the tank completely safe, even in extreme situations such as a road collision or a car fire. The tried and tested multivalve is OCTOPUS.
3. Gas line
thermoplastic or copper tube that connects the tank to the solenoid valve.
4. Gas filler with check valve
allows you to fill the tank with gas. Today, the standard is practical placement under the fuel filler flap, although some people prefer to have it in the rear bumper (often found in older LPG installations).
5. A solenoid valve
opens or closes the flow of liquid gas. It is installed when the reducer does not have an integrated solenoid valve. We recommend the LPG-MAX gas valve.
6. Liquid phase gas filter
integrated with the regulator or mounted separately. Filters liquid gas.
7. Reducer (evaporator)
is responsible for the gas pressure stability during engine operation. Usually comes with an integrated gas valve. Reducers are selected according to engine power.
8. The volatile phase filter
uses the centrifugal force of the expanded gas in the gaseous state to eliminate fine impurities and centrifuge the oily fractions present in the gas. It is mounted in front of the injectors. We use the Ultra360 ° filter known on the market in our installations.
9. Mapsensor
integrated gas pressure and temperature sensor. It provides data to the controller in order to make corrections to the injectors. Mapsensor PTS-01 will work here.
10. LPG Injectors
injectors assembled individually or combined in a set. They inject precise doses of gas into the suction manifold channels. We recommend the flagship Barracuda or FLIPPER injectors.
11. Controller
the brain of the entire autogas installation. Advanced computer controlling the operation of all system components. The following drivers will work great here: OPTIMA nano, OPTIMA EXPERT and OPTIMA PICO.
12 . The control unit (petrol / gas switch)
shows the current gas level in the tank and allows you to select the fuel on which the engine is to run. See RGB switch .
Advanced autogas technologies
The components of the installation are armed with intelligent electronics that control the gas all the way from the tank to the engine.
- The multivalve combines up to 7 mini-valves that ensure the 100% safety of LPG use? These are: solenoid valve, fire valve, overflow valve, pressure relief valve, manual operating (service) valve, check valve and 80% fill valve.
- The regulator has a casing temperature sensor > (not to be confused with a solenoid valve!). Have you ever wondered why the controller switches the power from LPG to petrol while “bottling” on a cold engine? No, nothing’s broken. If a large dose of liquid fuel consumed is too low temperature, the reducer sends a signal to the controller quickly – “The gas is still too cold, I won’t have time to evaporate! Switch to petrol!”.
- Control unit used in the 4th generation installation has the function of automatically starting the engine on petrol. Only when the engine reaches the right temperature, the controller switches the installation from petrol to gas.
- Mapsensor measures the pressure of the gas fed to the injectors, as well as the vacuum generated in the intake system. It transmits data to the control computer, which corrects and selects the appropriate gas injection times.
- Most of the 4th generation installations have the option of emergency start of the engine on gas in the event of a fault in the gasoline system. The operation scheme varies depending on the manufacturer of the installation.
Summary
As you can see – the 4th generation of LPG installations is very smart and secure system. Advanced electronics, rigorous testing of parts, the best materials and maturity on the market mean that sequential autogas injection, despite the existing next generations of LPG installations, remains the most installed in the world. See for yourself and choose the ALEX set. The list of recommended workshops can be found at alexlpg.com/en/find-a-lpg-workshop/